|
|
- Project Definition
- Common concepts and abbreviations in project control
- Detailed schedule and work progress basics
- Deviations and delays in the Project Time schedule
- Replan in the Project Time schedule
- Earned Value Management(EVM)
- The DCMA 14-Point Assessment in the Project Time schedules
Project Definition
A project can be defined when it has a specified start and end time, duration, and resources. A project consists of people with different skills who come together at a specific time and place to achieve the goals of the project with the least amount of time and money.
Project control and management knowledge synchronizes skills, tools, and techniques to achieve project goals. Project control is a professional and conscious performance in a set of engineering and specialized skills that is very important in the form of cost control and scheduling to achieve successful results in the project.
Project management must be aware of the principle and precise control of the project. Accordingly, a project control specialist is always associated with measuring and monitoring control variables.
Among the main differences between control and project management are the following:
Project control is a subset of project management with a primary focus on cost management and project planning. It produces the project by providing up-to-date information about the project in the form of periodic reports including obstacles, problems, costs, and financial and physical progress in return for the programmatic progress, while the project management receives the information and makes the final decision for the project.
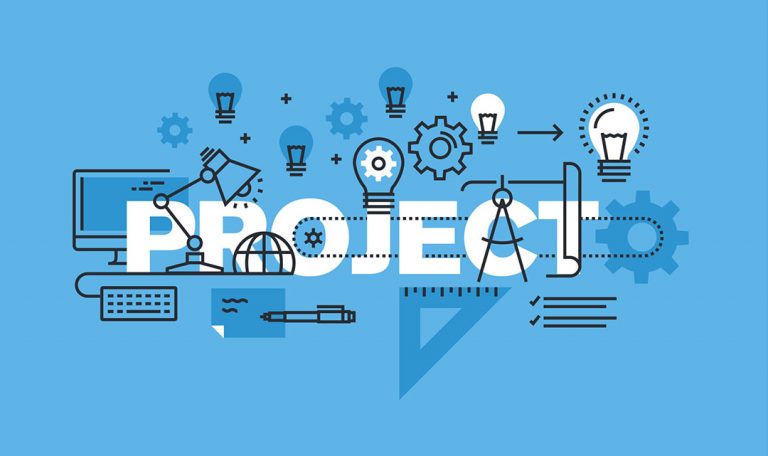
Among the common concepts and abbreviations in project control, the following can be mentioned:
1- PCWBS (Project Control Work Breakdown Structure) : The physical structure of deliverable items means the outputs delivered at the end of the project, which can be products, equipment, machinery, facilities, hardware, software, instructions, and documents, or a combination of them, and are always defined by nouns rather than verbs.
2- FWBS (Functional Work Breakdown Structure) : Operational structure of the project division of labor: It is prepared based on the project work description and includes a hierarchical and level-to-level breakdown of the operations of a project, which means the operations, efforts and energy in different specialized categories that will be required to obtain the deliverable items of the project. The project should be categorized into several completely distinct stages, and since all the output activities in each stage are the input to the next stage, all changes in each stage should be under control and are always in the form of verbs and not nouns.
3- RWBS (Responsibility Work Breakdown Structure) : Assign responsibility for the execution of operations related to the deliverable items of the project.
4- WBS (Work Breakdown Structure) : The breakdown structure includes all project activities for work planning including PCWBS and FWBS.
5- CBS (Cost Breakdown Structure) : It means the cost breakdown structure. In fact, CBS is the same as the Failure Structure (WBS) in which the cost of each of the elements in the Failure Structure is determined.
6-BOQ (Bill Of Quantity) : The workloads calculated in engineering degrees are in each department and discipline and can be the basis for failure at the lower CBS levels.
7- Baseline : The basic schedule is the formulation of what should be done in the future and at specific times.
8- Master Schedule Project: Macro schedule, which includes the general schedule of the project work stages.
9- Project Detail Schedule : The detailed schedule, the macro plan of each stage is broken down into more detailed levels (according to the structure approved by the employer).
10- Reschedule : Updating the program, modifying the program within the framework of the grand plan.
11- Re Plan: Revision of the plan, modification of the plan if the project is not completed on time.
12- Catch up Plan : Compensatory Schedule. The schedule has been created to compensate for the delay.
Detailed Schedule and Work Progress Basics:
After producing the detailed schedule and obtaining the critical routes and buoyancy times, by providing the necessary periodic reports of the achieved progress, the detailed plan will be updated and possible delays will be compensated within the framework of the key dates of the Key Events & Milestones program within the buoyancy time range of the work.
The detailed executive schedule should be prepared within the framework of the general schedule headings attached to the contract and up to the level of micro-forecasting required by the employer and using MS-PROJECT or Primavera software, which will include a network of CPM critical path activities. The approved detailed plan will be the basis for the implementation of the work and the control of the progress of the work (the contractor). The minimum provisions and requirements of the schedule and the basis for the progress of the detailed work include (but are not limited to) the following:
1. WBS Structure and Weights Associated with Each Activity Based on the Contract and Workload Volumes (Project PMS Structure).
The schedule should include the lower (end) levels of the WBS depending on the size of the project.
2. The correct and logical sequence of all the activities (predecessors) should be included in the schedule.
3. Documents, documents, resources, equipment, permits and other facilities that will allow the execution of the work to be included in the schedule.
4. The schedule must include a working timetable. Holidays and working hours during the implementation of the project should be precisely specified in the program calendar.
5. It should have a complete Resource Sheet. If this is not possible, the resources should be considered as estimates.
6. It must contain full (Resource Usage).
7. During the progress of the project, the contractor is obliged to update the schedule on a weekly and monthly basis in such a way that there is no change in the key dates as well as the completion date of the project.
8. Other documents that are the basis for controlling the progress of the work and must be provided by the contractors are:
Cash Flow Diagram
Histogram of the machine required
Histogram of the required manpower for different specialties
Histogram of materials and goods
What is deviation?
The difference between the numerical value of a programmatic progress and the actual progress of the project is called a deviation. In other words, suppose that the numerical value of the project's programmatic progress is 70 percent and the actual progress of the project is 30 percent, this project is 40 percent deviation from the initial schedule. (Negative deviation). It should also be noted that with only two numbers, the percentage of programmatic progress and the percentage of actual progress, it is not possible to comment on the amount of delay of the project, considering that the deviation is often of the type of the percentage of progress.
What is latency?
The difference between the end date of the schedule in which the actual information is entered and updated (in Primavera Schedule and in Microsoft Project Rescheduled) and the end date of the base program is called delay. The delay is in the form of the day and not in the form of the percentage of progress. Therefore, the statement "Project A is 10 percent late" is a wrong statement.
Let's say you're working on a project with a contract period of 12 months. The start and end of the project is on March 19. That is, the programmatic end date of the project is March 20. Now, suppose you have updated the schedule at the end of March. That is, in the initial program, you enter the actual start dates and actual progress percentages and schedule the program, assuming that you do not have a specific stipulation at the end of the program. After scheduling the program, the end date of the project will be on May 31. In this case, your project is 60 days late. The two months of April and May are the time period for the delay of the project.
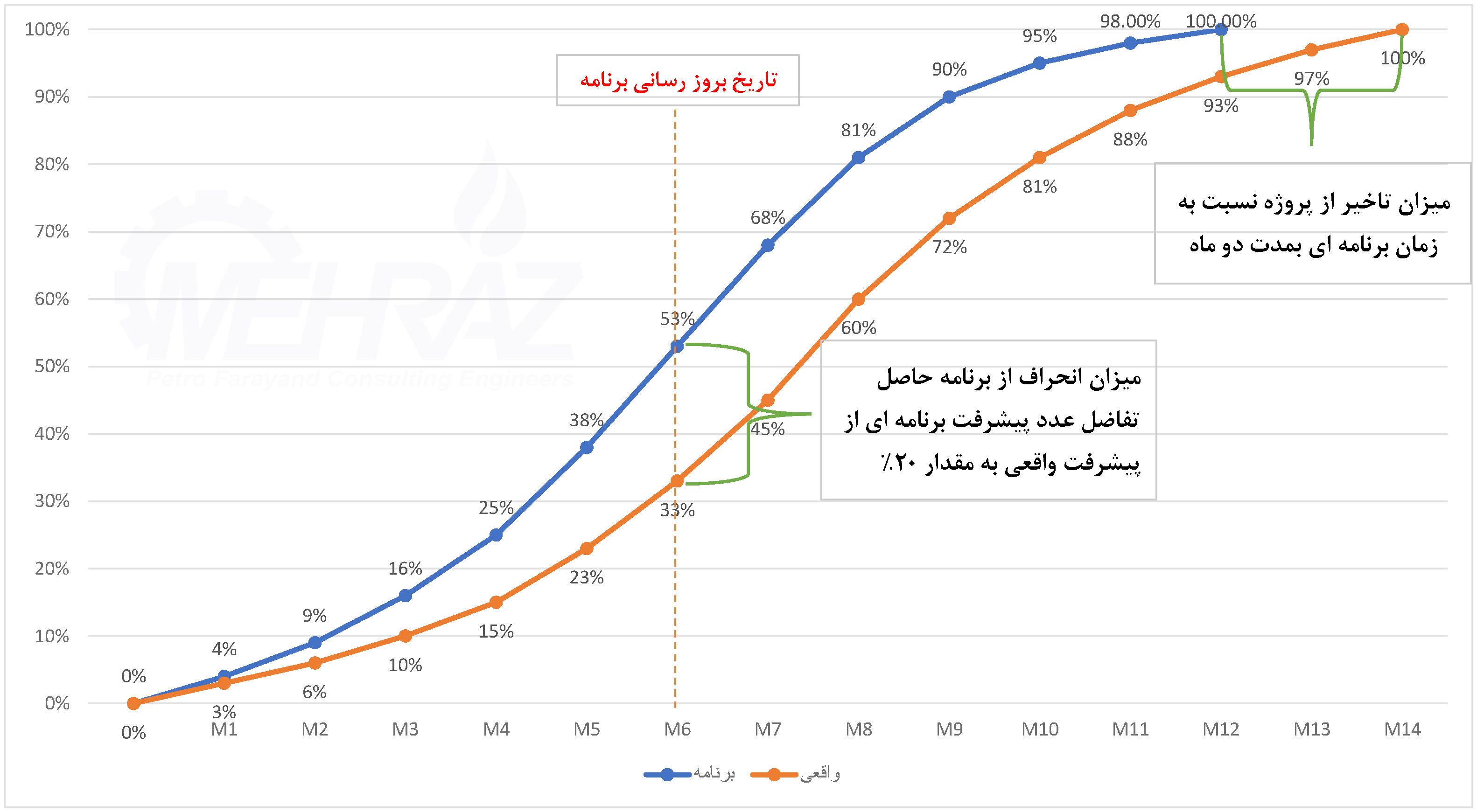
What is the relationship between delay and deviation?
Project deviation and delay are not necessarily related to each other, in other words, a project may not deviate but have a delay or a project may have a deviation but not a delay. The progress number of the whole project and the amount of deviation of the whole project is calculated independently of the relationships between the activities and the critical path of the project. That's why, in some cases, they calculate the actual and programmatic progress of the project and how much it deviates in an Excel file where there are no relationships between the activities. However, the calculation of the delay is completely and 100% dependent on the relationships between the activities as well as on the critical path of the project.
In other words, the actual progress number may be higher than the programmatic progress number, but there is a delay in the program. This occurs when critical activities have not been carried out and in contrast to a large amount of non-critical activities have been carried out. This combination occurs when all critical activities have been performed, but some non-critical activities have not been carried out as planned.
Re-plan in the project schedule:
A re-plan is done when the difference between the actual progress percentage and the initial baseline is very large, and it is not possible to complete the project at the contractual time, in which case a new schedule is prepared according to the real information of the project and the completion of the project is considered on a new date that is agreed upon by the employer, which is also called a re-plan.
The main challenge in replenishing the program is to equalize the percentage of program progress with the actual one, so that at the time of replenishment, we encounter 3 examples of activities:
1. Completed activities that have been completed with 100% real progress that we will have nothing to do with these activities.
2. Unstarted activities that have zero real progress percentage.
3. Ongoing activities in progress, some of which have been carried out and the percentage of real progress has been taken, and some of them remain unfinished.
In program re-planning, the program's progress percentage should be equal to the actual on the third option activities, which include In Progress activities.
Scurve Progress Chart Failure:
At the time of the Re-plan in the S curve graph, the failure will be created so that the progress chart of the Plan at the Re-plan point should be equal to the percentage of the actual progress, and the calculations of the new progress of the program will start from that point. This will also happen in the Program Progress column in P6 and MSP software, so that the program progress numbers in the Schedule Progress column should be equal to the actual Performance Progress column and the progress numbers of these two columns should be equalized. Then, by rescheduling in the software, the extension of the end time of the program will be determined in the software according to the program relationships in the unfinished activities, and by changing the durations of the remaining activities and the lags of their relationships, we should reach the time approved by the employer. At the end we will get a Baseline of the re-planned program.
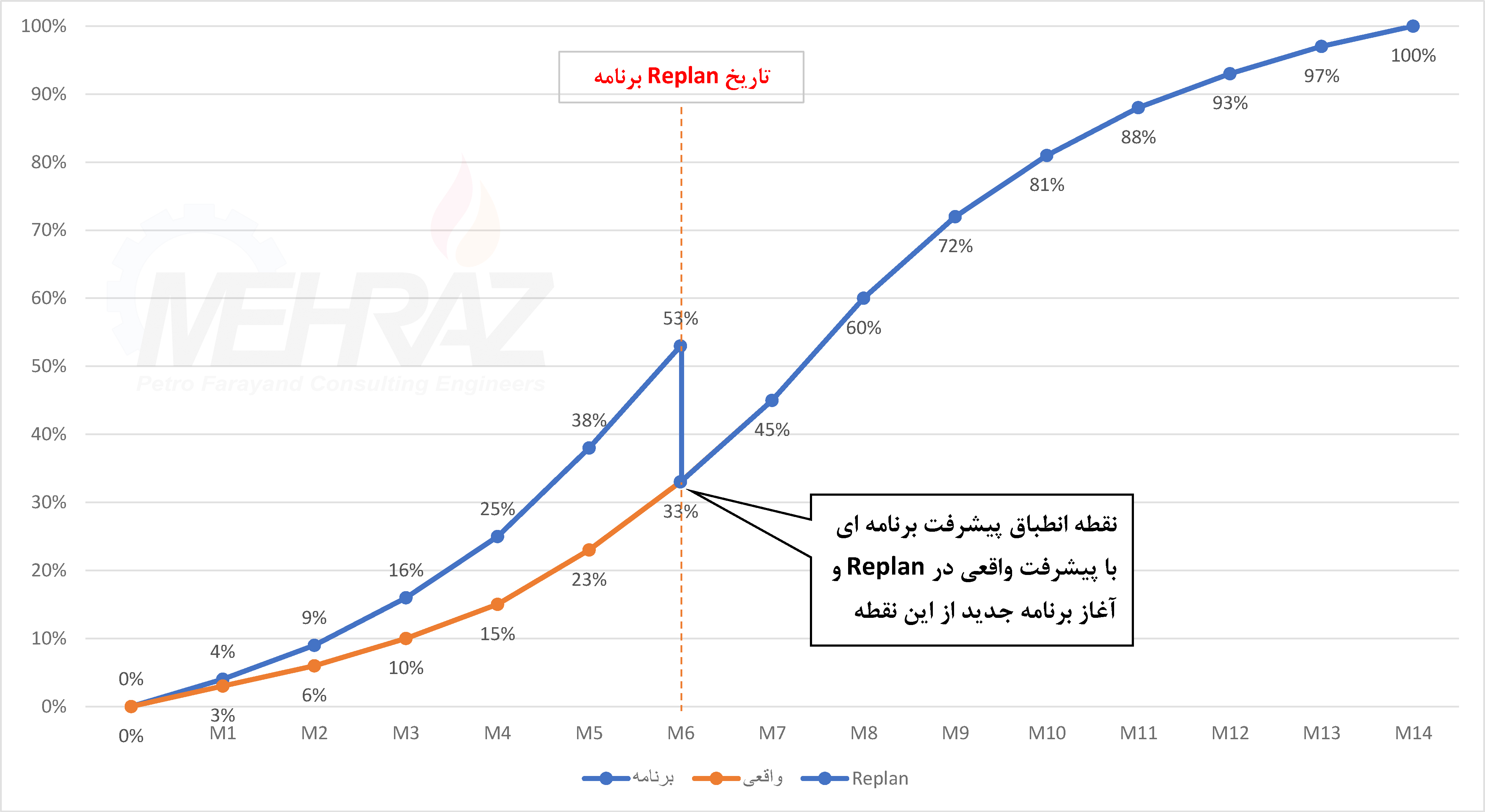
In P6 software, the actual progress percentage number in the Performance %Complete column cannot be copied in the Schedule %Complete column, which shows the program progress percentage, due to the fact that it is not possible to enter the number manually in this column and calculates the program number according to the formula set in the software. However, it is possible to get a number close to it by taking the Baseline from the program itself, and for this it is necessary to first make the adjustments according to the path and the following image:
admin –> admin preferences -> Earned Value
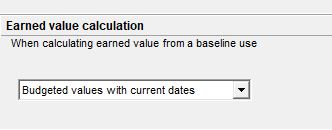
Then close the top window and take the Maintain Baselines section of the Baseline program in the Project tab and assign it in the Assign Baselines section.
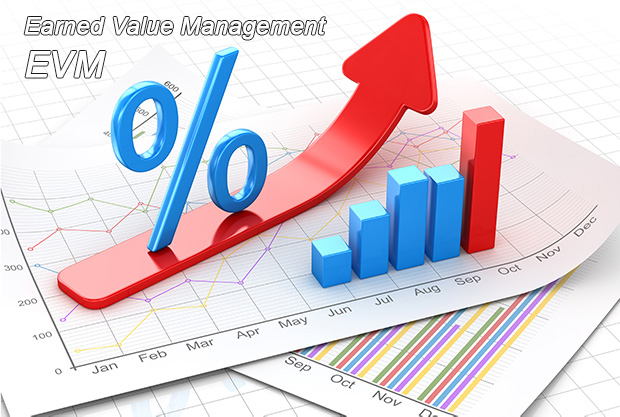
Earned Value Management (EVM)
Earned Value Management is one of the methods of project management, which controls and manages the project based on financial and cost progress. The value earned EVM has the following three parts:
Planned Value: Also known as BCWS, it stands for Budget Cost of Work Schedule, which means the planned value (budget) for activities that are to be completed by the specified date.
Actual cost: The actual cost is the sum of the costs spent until the completion of the project. Cumulative AC is the total actual cost of activities performed up to the end of a given period of time, such as days, weeks, months, or years.
Earn Value: Another name is BCWP, which stands for Budget Cost of Work Performed, which means the cost of planning activities that have actually been performed.
.jpg)
Steps to implement the earned value management technique:
1. Identifying and defining the failure structure of activities
2. Defining the relationships of activities and their timing
3. Allocating resources to activities, and calculating costs
4. Analyze all the data and prepare the schedule of the whole project
Basically, performance appraisal always makes sense by analyzing the earned value. Software such as P6 and MSP are defined with such an approach. The index that represents the actual performance in these systems is called Earn value. The Planned Performance Index is also Planned Value, which is abbreviated by EV and PV, respectively. In P6 software, the Performance % Complete and Schedule % Complete fields are the percentage representation of EV and PV, respectively.
Cost Performance Index (CPI):
This index is equal to the ratio of EV earned value to actual AC costs, which determines how well the actual costs were proportional to the initial planning. If this value is equal to one, it means that the real costs are appropriate, and if it is less than one, it means that the value gained is less than the real cost, and in fact, the over cost has occurred, and in the future, the project may lose money.
CPI = EV / AC
Also, instead of the ratio of these two values, the difference between them can be calculated, which is called CV (Cost Variance), and if the resulting values are negative, it indicates the excess cost in the project.
CV = EV – AC
CPI and CV indicators show the state of financial performance. There are similar indicators for assessing the status of temporal performance. Such as the SPI (Schedule Performance Index) index, which is the result of the ratio of earned value to planned value.
SPI = EV / PV
If this value is equal to one, it means that the execution and planning match, and if it is greater than one, it means that the work done is ahead of schedule.
The SV (Schedule Variance) index, similar to the CV index, is obtained from the difference between the earned value of EV and the planned value of PV.
SV = EV – PV
In all earned value indicators, the EV index is compared with the actual cost and the planned cost, and the actual and planned cost are never directly compared to each other.
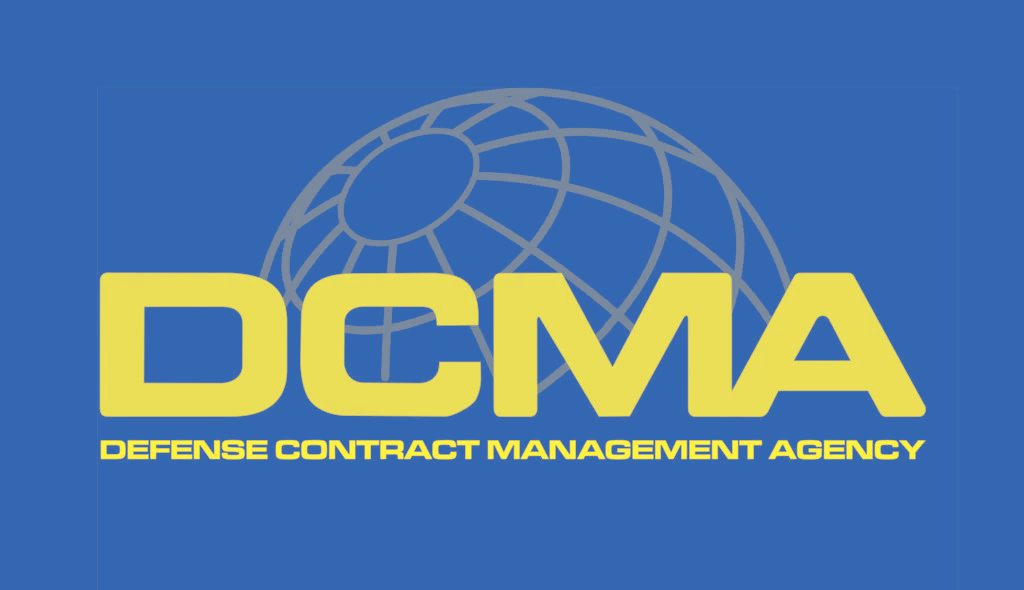
The DCMA 14-Point Assessment
1. Schedule Logic (Logic): We call a logical program in which the prerequisite relationships are fully defined and the critical path is well identified. One way to evaluate this issue is to allocate a sufficient amount of prerequisite relationships in the program, and in a word, the program should not have open-ended activities, preferably not exceeding 5% of these activities. (All activities must have at least one prerequisite relationship and one post-need relationship.)
2. Prerequisites with Negative Lag or Leads: It is a control metric that helps measure the percentage of activities that have a negative lag between each other. Specifically, the term specifies the overlapping time between two activities in a project plan. In other words, it indicates the exact time of the start of an activity before the end date of the previous activity (prerequisite), which overlaps. Leads in the program should be zero, so that there are no activities with negative latency between each other. Otherwise, by causing more failures, activities with relationships can be defined without time delay. This metric can prevent critical trajectory analysis.
3. Positive Delays in Defining Prerequisite Relationships (Lags): In particular, it allows for the assessment of the percentage value of project activities that have a positive latency between each other. This metric actually shows the calculated time (hour/day) when a particular activity starts after its previous period end date.
DCMA is more flexible for this metric than Leads, recommending that the lag in the project schedule should not be more than 5%. However, excessive use of lags can also cause an obstacle to critical path analysis, so it is recommended to avoid using them. A good way to replace using this metric is to create activities with more failures.
4. Types of relationships: It is recommended that 90% of project scheduling activities be of the finish-to-start (FS) type. Relationship (FS), provides the most explicit representation of project schedule activities. Other types of relationships in a schedule include finish-to-finish (FF), start-to-start (SS), and start-to-finish (SF). Although it is possible to use a variety of prerequisite relationships in all software systems such as Primavera P6 or Microsoft Project, it is not recommended to use them and it is better to use the finish-to-start (FS) type of relationship by breaking down the activities appropriately.
5. Hard Constraints: Time constraints in the project schedule include Mandatory Start and Mandatory Finish and Soft Constraints (As Late As Possible, Start On, Start On or Before, Start On or After, Finish On, Finish On or Before and Finish On Or After).
DCMA recommends that 5% of the constraints used be hard constraints because they can cause problems in the application. Hard constraints can prevent the app from being logic-driven and create negative lags in the app. In other words, hard constraints should be avoided due to the inability to create a logical natural flow in the program and the impossibility of correct calculations in the creation of the Critical Path Method. Soft constraints, on the other hand, allow scheduling to be logic-driven and are not essential to scheduling.
6. Creating Long Floats (High Floats): This metric calculates the percentage value of unfinished work with a total float greater than 44 working days. DCMA requires that the High Float of activity does not exceed 44 business days, i.e., the percentage of total unfinished work does not exceed 5%.
This metric shows the time (hours/days) that an activity can be delayed without negatively impacting the project's milestones or estimated project completion time. A given job with a total float of more than 44 business days can be the result of activities with incomplete (predecessor/successor) relationships. As in timing software such as Primavera P6 and MSP, the total buoyancy is calculated based on the critical path method. If the activities have a long float, it indicates that there is not enough and correct prerequisite relationship.
7. Negative Float: This criterion is related to hard constraints because it can indicate the assignment of hard constraints to timing. When this happens, it is very possible that the completion of the project or the realization of the milestones will be delayed.
The DCMA acceptable range for this criterion is zero, so it is necessary to conduct regular project schedule checks in order to avoid negative floating, as if tasks with a large amount of negative float should be reduced. After the Baseline is created and the application is updated, a negative buoyancy may be generated based on the intended constraints (Mandatory Finish in Primavera P6), in which case the negative buoyancy can be considered a delay in the schedule.
8. Estimated Long Duration for Activities: Recording activities over a long period of time usually increases the risks of the project and also prevents the identification of the correct prerequisite relationships. It is better that the majority of activities in the schedule are well broken. Of course, some activities, such as the process of manufacturing, supplying equipment, long delivery, and outsourcing in the project, cannot really be broken and can be considered a goal such as 5% or 10%. Of course, a threshold should be provided for the identification of long-term activities, so that the activities with a long duration do not exceed more than 5% of the project activities.
9. Invalid Dates: After the schedule has been updated in the date (Data Date in Primavera P6) or (Status Date in MSP) to the scheduled dates before these dates or the actual dates thereafter, invalid dates are said to mean that the foreseen or unfulfilled work should not be in the past and the actual or completed work should not be placed in the future. Therefore, invalid dates are not allowed under any circumstances, and this avoids irrational situations in which the foreseen work is planned for the past and the actual work has happened in the future.
10. Allocation of Resources: Loading resources into the program is not a requirement, but DCMA tends to prepare a schedule with resources and costs, in which case a complete schedule is developed and all activities except milestones must have associated resources or costs.
11. Missed Tasks: This index looks at the number of activities that have been completed late compared to Baseline's date, which can cause the project to fall behind or prevent it from continuing. This indicator helps to assess the efficiency of the schedule in parallel with the Baseline and how well the project schedule matches the Baseline schedule.
Missed tasks can be caused by insufficient resources, poor planning, or more. As a result, DCMA believes that the number of such activities should not exceed 5% and that if they become critical, a revision and modification of the schedule will be required.
12. Critical Path Test: In a critical pathway, there must be a continuous link from Milestone at the beginning of the project to Milestone at the end. In this test, the integrity in the critical path and the establishment of a good logical link in the schedule are evaluated.
13. Critical Path Length Index (CPLI): The Critical Path Length Index (CPLI) evaluates the efficiency and efficiency required to complete and complete a project on schedule. This index measures the ratio of the sum of the critical path length of the project and the total float of the project to the length of the critical path of the project. The length of the critical path is equal to the time of working days from the current date to the completion of the project. The target number in CPLI is 1, which means that the project must be completed within the scheduled time. Schedules where the CPLI is less than 0.95 indicate that the project is inefficient and needs further investigation. However, if the CPLI is above 1.00, it indicates that there is a timeline margin and the project may be completed earlier than planned.
14. Program Execution Index or Activity Completion Rate according to Baseline (BEI-Baseline Execution Index): The Baseline Implementation Index (BEI) test is a measure of evaluating program performance in parallel with the Baseline program, but focuses on the productivity of the project team in the process of executing activities. This indicator provides the ratio of completed activities to the number of tasks that should have been completed according to the baseline.
Similarly, like the Critical Path Length Index (CPLI), the DCMA for the Index Test (BEI) is an acceptable limit of 1.00, which indicates that the project team is performing well and according to schedule. When the BEI exceeds 1, it indicates that the team is acting ahead of schedule, while when it falls behind 1, it means that it is behind schedule.
|
|
|